The Benefits of Using Self Clinching Fasteners in Industrial Applications
Jul 28,2025
In industrial applications where precision, durability, and efficiency are paramount, self clinching fasteners have emerged as a game-changing solution. These specialized components offer a multitude of benefits that address the unique challenges of heavy-duty manufacturing, assembly, and operation across diverse sectors.
One of the primary advantages is their ability to streamline automated production processes. Unlike traditional fasteners that often require manual handling, threading, or welding, self clinching fasteners integrate seamlessly with automated press systems. This compatibility reduces reliance on manual labor, minimizes human error, and accelerates assembly lines—a critical factor in high-volume industrial settings such as automotive manufacturing or appliance production. By enabling rapid, consistent installation, they contribute to shorter production cycles and higher output rates, ensuring industries can meet tight deadlines and scaling demands.
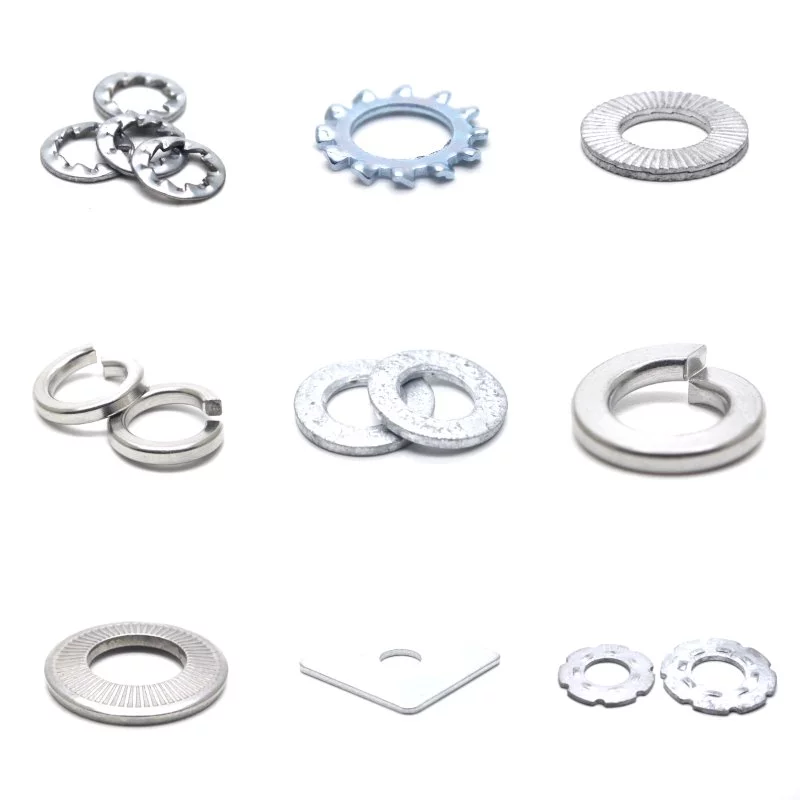
Self clinching fasteners also enhance connection reliability in harsh environments. Industrial settings are often characterized by extreme conditions, including high temperatures, heavy vibrations, chemical exposure, and mechanical stress. These fasteners, crafted from robust materials like stainless steel or heat-resistant alloys, maintain their integrity under such duress. The cold flow mechanism during installation creates a permanent interlock with the host material, eliminating loosening even in vibrating machinery or equipment subjected to constant movement. This reliability is invaluable in sectors like aerospace, where loose components could compromise safety, or in chemical processing plants, where secure connections prevent leaks and contamination.
Another key benefit lies in their material versatility and corrosion resistance. Industrial applications frequently involve contact with moisture, chemicals, or outdoor elements, making corrosion a significant concern. Self clinching fasteners are available in a range of corrosion-resistant materials, including passivated stainless steel and zinc-plated carbon steel, as well as specialized coatings for extreme environments. This adaptability ensures long-term performance in sectors such as marine engineering, where saltwater exposure is constant, or in food processing, where hygiene standards demand resistance to cleaning agents. Additionally, their compatibility with various base materials—from aluminum to high-strength steel—allows engineers to select the optimal combination for specific load and environmental requirements.
Cost efficiency is also a standout advantage in industrial contexts. While the initial investment in self clinching fasteners may be marginally higher than traditional alternatives, their long-term savings are substantial. The elimination of secondary operations like welding or threading reduces labor and material costs. Their durability minimizes maintenance and replacement needs, even in high-wear applications such as conveyor systems or heavy machinery. Furthermore, the precision of their installation reduces the risk of rework or product failures, which can incur significant expenses in industrial-scale production. Over time, these factors contribute to a lower total cost of ownership, making them a cost-effective choice for budget-conscious operations.
PREVIOUS: